Une DSI au coeur du process industriel : la recette secrète des Cuisines Schmidt
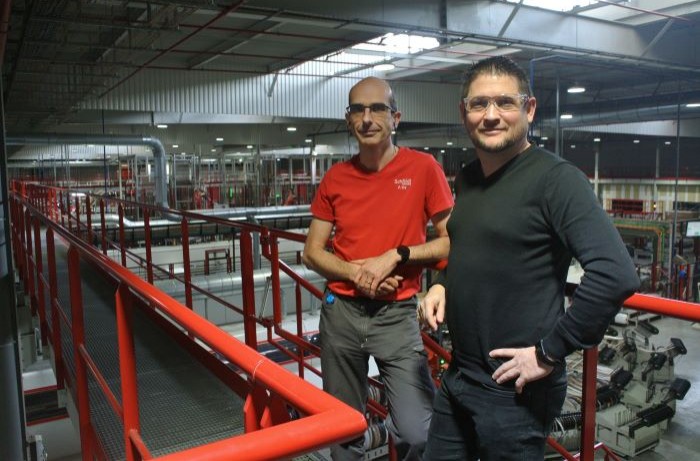
Au fil des ouvertures de nouvelles lignes de production, le cuisiniste Schmidt Groupe a poussé l'intégration entre informatique de gestion et informatique industrielle. Aboutissant à un process fortement automatisé, grâce à des logiciels maison adaptés à sa production à la commande et sans stock.
PublicitéDès les premiers pas dans l'usine U3 de Schmidt Groupe, un atelier de l'industriel situé à Sélestat et dédié à l'ameublement, le haut niveau d'automatisation de la ligne de production saute aux yeux : des bras robotisés saisissent des panneaux de bois, les plaçant sur des machines spécialisées dans la découpe, le plaquage ou le perçage avant que d'autres ne les déposent dans un stockage vertical intermédiaire, selon un arrangement bien précis calculé par un algorithme afin d'optimiser l'opération suivante.
Dans ce qui reste une activité de menuiserie, les interventions humaines sont peu nombreuses. Comme l'expliquent Daniel Freyd, le DSI de ce groupe de plus de 1900 personnes, et Patrick Viry, le responsable automatisme et informatique industrielle, le virage vers l'automatisation remonte à 2008. « A l'époque, la robotisation était peu présente au sein de nos ateliers. Mais, lors de la crise de 2008, nous avons profité du fait que les fournisseurs de robots cherchaient à se diversifier », raconte le DSI. Le cuisiniste installe ainsi 18 robots dans son atelier U2 à Sélestat (Bas-Rhin), ville hébergeant son principal site industriel qui regroupe aujourd'hui environ 1000 personnes.
Maîtriser la donnée de bout en bout
Pour U3, une dizaine d'années plus tard, le total monte à une quarantaine de robots. Puis à une soixantaine pour U2B, ouvert en 2019. Et Schmidt Groupe prévoit d'en déployer plus de 80 pour sa future usine (U3B), toujours sur le site de Sélestat (voir encadré). « Grâce à cette automatisation, nous sommes plus flexibles en intralogistique et avons apporté de nouvelles fonctions, reprend Patrick Viry. Le tout en continuant à faire croître le nombre d'opérateurs, qui est passé d'environ 650 en 2009 à plus de 730 aujourd'hui. »
La machine dédiée au plaquage des champs. Le cuisiniste a travaillé avec les fournisseurs de machines - ici IMA Schelling Group - pour adapter leurs outils à ses process. (Photo : R.F.)
La face cachée de cette production où 95% des pièces échappent désormais à un processus de menuiserie traditionnel, c'est évidemment le logiciel. Et ce dès l'amont, soit lorsqu'un projet de cuisine ou d'aménagement intérieur est enregistré chez un des concessionnaires du cuisiniste, sur des logiciels fournis et maîtrisés par le groupe. « Un des rôles de la DSI consiste à former et équiper les 6000 utilisateurs de notre réseau de vente, détaille Daniel Freyd. Car la clef de notre efficacité réside dans la maîtrise de la donnée de bout en bout. » Selon le DSI, Schmidt Groupe, investit en moyenne 50 M€ par an dans son outil industriel, dont 5 ou 6 dédiés à l'informatique supportant ses process de fabrication.
Publicité
Entre deux étapes clefs (découpe, plaquage, perçage, emballage), les pièces sont réordonnancées par des bras robotisés pour optimiser la suite du process, en fonction d'algorithmes maison. (Photo : R.F.)
Autre exemple de ces ré-ordonnancements en intra-logistique, les pièces sont ici stockées dans de grands racks verticaux (à droite) afin d'optimiser la phase d'emballage. (Photo : R.F.)
Dès la prise de commandes, l'industriel confirme une semaine de livraison, associée à des pénalités si cet engagement n'est pas tenu. Quelques semaines avant la fabrication, les données de cette commande sont ensuite transmises par le concessionnaire au groupe et déversées dans SAP. Le premier mécanisme alors mis en oeuvre vise à optimiser les transports, afin de définir la journée de production des meubles faisant partie de la commande. « Puis, vient se greffer une seconde logique, celle de l'optimisation de la matière, qui débouche sur un réordonnancement de la production », précise Daniel Freyd.
Optimisations en intra-logistique
Si la planification est effectuée dans une solution du marché (Delmia Quintiq de Dassault Systèmes), les autres composantes logicielles résultent, elles, de développements maison. C'est le cas des briques de MES qu'exploite le cuisiniste, comme des algorithmes d'optimisation de la matière, essentiels en intra-logistique. « C'est là que réside notre savoir-faire en ingénierie », souligne Patrick Viry. Le fruit du travail d'une équipe d'une douzaine de personnes au sein de la DSI et du service automatisme et informatique industrielle, qui en compte une vingtaine. Car si la finance, le contrôle de gestion et la logistique sont gérés dans SAP, toute la logique de décomposition des commandes pour l'outil industriel est prise en charge par des logiciels spécifiques. Via d'abord ce que les équipes de l'industriel appellent le configurateur, outil qui chaque nuit décompose les commandes avec des règles propres pour venir nourrir les algorithmes d'ordonnancement de l'appareil industriel. « Car nous gérons un système sans gamme, ni nomenclature, qui génère trop de combinatoires pour une solution standard du marché », souligne Daniel Freyd.
Pour déplacer ses lots de panneaux, l'industriel a recours à des AGV (Automatic guided vehicle soit un robot se déplaçant automatiquement). (Photo : R.F.)
Pour ce dernier, le passage d'une logique de petites séries à un process industriel ne produisant que le nécessaire, sans stock, est issu d'une impulsion donnée par la direction générale du groupe dès la fin des années 90. Et d'un voyage d'études au Japon, auprès des industriels de l'automobile locaux. Une source d'inspiration, mais un modèle impossible à dupliquer dans le contexte du cuisiniste. « Notre modèle est plus pointu et suppose une exploitation de la donnée dans la machine industrielle et un jalonnement précis pour arriver à avoir un camion chargé comme attendu le jour J », explique le DSI. Sans oublier la capacité à réordonnancer la production du jour à la volée pour réagir aux événements imprévus sur la ligne.
Trop interdépendants pour ne pas travailler ensemble
L'intégration entre informatique de gestion et informatique de production résulte aussi de la proximité entre la DSI, qui regroupe 85 personnes, et le département informatique industrielle et automatisation. « Je viens de cette dernière, raconte Daniel Freyd, arrivé dans le groupe en 2002 et à la tête de la DSI depuis 5 ans et demi. La DSI s'attache à bâtir des ponts avec l'informatique industrielle sur tous les sujets clefs : la sécurité, le réseau, la robustesse de la production... Aujourd'hui, des processus communs aux deux départements assurent le patching des machines ou encore la présence d'un EDR jusqu'au fin fond des usines. » Un renforcement de la cybersécurité qui accompagne l'ouverture du réseau des usines vers l'extérieur, par exemple pour consolider les données IoT sur le cloud. « Nous avons effectué des bonds de géant ces dernières années, en dépassant la séparation entre IT et OT (Operational Technologies), abonde Patrick Viry. Nous avons dépassé le concept de la machine autonome sur la ligne de production, la DSI et l'informatique industrielle sont trop interdépendantes pour ne pas trouver des solutions communes. »
La logique de production du cuisiniste repose sur une maîtrise de la donnée de bout en bout, de la commande à la livraison. Induisant une proximité entre informatique industrielle, représentée par Patrick Viry (à gauche), et la DSI, pilotée par Daniel Freyd (à droite). (Photo : R.F.)
Si la ligne de production est largement automatisée, des opérateurs restent en charge du pilotage des opérations et du contrôle qualité. « Avec un rôle de maintenance de l'installation, précise Patrick Viry. Or, les lignes de production sont étendues, les opérateurs ne peuvent pas être au courant des événements affectant l'ensemble du processus. » En amenant l'information sur les dérives en cours ou les pannes au plus tôt aux opérateurs, le cuisiniste est parvenu à gagner 4 points de taux d'utilisation de sa ligne de fabrication, sur un potentiel identifié de 8 points de perte.
La GenAI à l'étude dans la maintenance
Si, au travers de ce cas d'usage, l'industriel déploie de premières applications d'IA - via des algorithmes de Machine Learning mesurant l'écart entre le fonctionnement théorique et le réalisé -, le DSI et son compère de l'informatique industrielle se montrent prudents quant au potentiel de la technologie dans leur contexte spécifique. « La détection d'une dérive est simple sur une production en série, mais dans notre process, la pièce change à chaque fois ! », souligne Patrick Viry. Si Schmidt Groupe a déjà développé des algorithmes permettant de surveiller l'état de fonctionnement des machines-outils et en prédire les pannes, Patrick Viry estime que l'investissement pour généraliser le déploiement de ces algorithmes n'est aujourd'hui pas justifié.
Reste l'IA générative. D'essence probabiliste, celle-ci ne présente pas d'intérêt dans le process industriel. Mais le DSI note son potentiel dans la maintenance, pour analyser rapidement, via une approche RAG, les documentations des machines ou sur les processus ainsi que les retours d'expérience suite à des pannes. « Mais nous n'en sommes qu'aux débuts », tempère Patrick Viry. Pas de quoi inquiéter un industriel habitué à travailler sur le temps long.
Article rédigé par

Reynald Fléchaux, Rédacteur en chef CIO
Suivez l'auteur sur Twitter
Commentaire
INFORMATION
Vous devez être connecté à votre compte CIO pour poster un commentaire.
Cliquez ici pour vous connecter
Pas encore inscrit ? s'inscrire