Renault Group sur la longue route du déploiement d'un WMS industriel
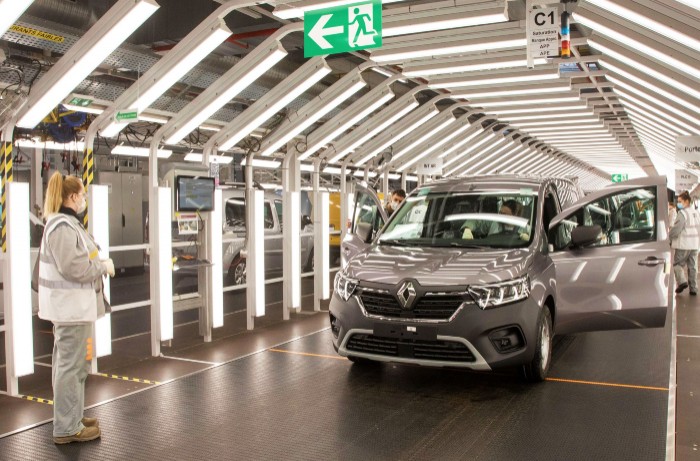
Pour concrétiser la transformation digitale de sa supply chain, le constructeur automobile français déploie et enrichit depuis 2018 un WMS industriel pour la logistique entrante de ses usines, avec Hardis Group. Renault Group a muté vers l'agile pour ce projet destiné principalement à optimiser en temps réel les espaces de stockage et les ressources de ses sites.
PublicitéRadouane Make, supply chain inbound process engineering manager warehouse, chapeaute une entité qui dépend de la direction supply chain, dont la fonction est de définir et mettre en oeuvre les processus de travail liés à la logistique entrante des sites de production et d'en piloter le changement. Il pilote en particulier la continuation du déploiement du WMS de Reflex (Hardis Group), projet qui s'inscrit dans le cadre du plan de transformation numérique de la supply chain. L'industriel a choisi l'outil en 2018 et contribue à adapter cette solution originellement destinée à la distribution, à la logistique industrielle, en collaboration avec l'éditeur.
C'est une longue route que celle de la digitalisation des entrepôts, en particulier pour un industriel comme le constructeur automobile français. « Dans un contexte industriel comme celui de Renault Group, le déploiement d'un WMS est bel et bien un enjeu central », insiste d'ailleurs Radouane Make. Le projet d'installation d'un nouvel outil, né il y a plus de 6 ans, en 2018, va encore se poursuivre durant plusieurs années. A l'époque, le constructeur automobile voulait « améliorer la gestion en temps réel des espaces de stockage et des ressources, gagner en fiabilité des stocks ainsi qu'en traçabilité, et automatiser certains processus ». Aujourd'hui, Renault Group est au milieu du gué avec 15 sites - principalement industriels, mais aussi logistiques - équipés sur 30.
Un WMS sur étagère adaptable à l'industrie
Avant ce déploiement, Renault Group disposait d'un outil de gestion de la logistique entrante développé en interne, mais devenu obsolète. « Nous nous sommes posé la question d'un nouveau développement interne ou d'un outil externe », raconte Radouane Make. « Mais il existait des solutions sur étagère qui répondaient en grande majorité au périmètre fonctionnel que nous avions identifié ». Il s'agissait en particulier de piloter en temps réel les espaces de stockage et les ressources. Par ailleurs, l'entreprise voulait une intégration de l'outil à son SI et davantage d'agilité et de rapidité de déploiement et d'évolution. « Nous avions le TMS de Shippeo, une solution maison de gestion des flux d'emballage, un ERP, un MES, etc. », résume Radouane Make. L'industriel a donc rapidement décidé de se tourner vers une solution externe.
« Dans un contexte industriel comme celui de Renault Group, le déploiement d'un WMS est bel et bien un enjeu central », dit Radouane Make, supply chain inbound process engineering manager warehouse de Renault Group (Photo : Renault Group).
Le constructeur a étudié plusieurs solutions du marché chez Manhattan Associates, Mecalux ou Oracle, par exemple. Il a finalement opté pour Hardis et sa solution de WMS Reflex. La filiale de Hardis Group, spécialiste de la gestion d'entrepôts logistiques, était qui plus est particulièrement intéressée par cette opportunité d'adapter sa solution à des sites industriels. Elle a effectivement lancé, en 2020, Reflex WMS for Factory. En revanche, Renault Group n'a pas souhaité disposer d'une version SaaS. « Nous sommes dans des usines, rappelle Radouane Make. Nous faisons un exercice en lien direct avec la fabrication des véhicules ». Un contexte où le cloud et le SaaS apparaissent pour l'instant trop risqués.
Publicité15 à 25% d'optimisation de l'espace
C'est entre deux confinements Covid que Renault Group a commencé à travaillé sur l'intégration du WMS à son SI, comme le raconte Radouane Make. Il a d'abord été installé sur le site de Maubeuge (Nord), voué à la production de véhicules électriques - dont le Kangoo 3 -, choisi comme site pilote. « Nous avons opté pour une démarche agile, précise-t-il. Nous avons dû changer nos méthodes de travail pour ce faire. Nous pilotons le projet par vagues trimestrielles de déploiement, avec des ajustements si nécessaire, pour toujours avancer ». La solution a été conçue et déployée en parallèle, pour que le changement soit le plus transparent possible pour les usines. « Dans la logistique de distribution, on peut basculer en big bang, pas dans la production. Nos sites tournent en 3/8, avec un calendrier très chargé ». Renault Group a d'abord défini un core model et travaillé en parallèle sur la définition enrichie de la solution.
« Nous avons défini les process nominaux sur lesquels nous venons intégrer ensuite de l'innovation ». Ce sont les leviers de performance identifiés par Renault Group pour sa digitalisation qui sont ainsi appliqués au WMS. Le premier réside dans la synchronisation des flux, par la connexion avec le MES pour la bascule en flux tirés (flux de production tirés par les commandes des clients) et la connexion au métavers et au jumeau numérique. Autre levier, la traçabilité des véhicules autonomes, jusqu'aux pièces détachées. 3e levier, l'automatisme, avec un WMS « prédisposé à communiquer avec les automates », comme le précise Radouane Make. Enfin, le coeur du projet : la gestion dynamique des surfaces. « Il s'agit de proposer une place dans l'espace d'entreposage en fonction des types de produits, de leur taille, du volume des palettes, etc. Nous arrivons déjà à optimiser l'espace de 15 à 25% », affirme Radouane Make.
14 usines équipées sur 30
Le WMS a donc été éprouvé dans un premier temps dans l'usine pilote et déployé dans trois ou quatre autres sites en parallèle. Le choix de Maubeuge et des premiers sites déployés s'est fait sur dossier de candidature, et en fonction du calendrier industriel des usines. « Pour obtenir le nouveau système, celles-ci doivent remplir un dossier et répondre à certains critères », précise Redouane Make. « Le niveau de qualité de la data ou de gestion EDI des avis d'expédition en font partie, par exemple. C'est aussi le cas de la maturité en matière de pilotage des flux ». Une fois ce premier niveau de sélection lié à la motivation et à la maturité digitale franchi, les sites candidats s'engagent sur un calendrier. « C'est une question de préparation et de synchronisation, parce que le projet n'est pas isolé, mais s'intègre dans la stratégie globale du groupe », rappelle Radouane Make. « Nous rédigeons un contrat de déploiement pour lequel l'usine s'engage à mettre à disposition les ressources nécessaires au projet. Nous avons installé 14 sites à ce jour, dont des plateformes logistiques, - en Europe, au Maghreb et en Amérique du Sud, dont Alpine à Dieppe, Douai ou encore Curitiba au Brésil - sur un total de 30. Et nous en avons prévu 3 autres en 2025 ». Avec cette méthode de déploiement progressif, Renault Group affirme aussi capitaliser sur les bonnes pratiques des premiers déploiements et ajuster en permanence sa façon de faire.
« Par ailleurs, ce projet touche entre 400 et 500 personnes par site, rappelle Radouane Make. Nous avons donc établi une méthodologie de déploiement, mais aussi de pilotage du changement ». Une démarche qui implique une montée en compétence des équipes sur la solution, pour que l'entreprise puisse s'appuyer sur des relais de déploiement locaux. Sans oublier que le constructeur déploie progressivement la solution dans toutes ses usines, installées sur différents continents, ce qui impose de s'adapter aux différentes cultures.
De la data en temps réel sur la supply chain entrante
Parmi les bonus du déploiement, figurent le travail avec les prestataires et la réduction de l'empreinte carbone. Renault Group met ainsi son WMS à disposition de ses prestataires sur un périmètre restreint pour de la gestion de stocks, par exemple. « Notre agilité nous permet d'intégrer ainsi un prestataire externe dans notre logistique sans nous perturber, précise Radouane Make. Mais, désormais, nous choisissons aussi des prestataires qui travaillent déjà avec ce type d'outils ». Du côté de l'empreinte carbone, le WMS conduit à une activité proche du zéro papier et à une gestion plus durable des emballages. « Dans une usine qui fabrique 130 voitures, j'étais à 7 tonnes de papier ! »
Enfin, pour l'avenir, outre la poursuite des déploiements, Renault Group envisage d'autres fonctions autour de son WMS, comme la synchronisation de flux, l'intégration rapide de nouveaux projets ou encore un système de drop-and-swap, par exemple, pour qu'un chauffeur dépose sa remorque et reparte, sans attendre le déchargement, avec une autre remorque, grâce à un YMS (yard management system). « C'est une architecture complexe, insiste Radouane Make. Mais elle permet entre autres de mieux gérer la pénurie de chauffeurs ». La solution déployée assure désormais également la récupération en temps réel de la data de la supply chain de production entrante. « Nous avons désormais une capacité de monitoring en temps réel de nos activités. C'est aussi la première brique nécessaire pour d'éventuels développements d'IA ».
Article rédigé par

Emmanuelle Delsol, Journaliste
Suivez l'auteur sur Linked In,
Commentaire
INFORMATION
Vous devez être connecté à votre compte CIO pour poster un commentaire.
Cliquez ici pour vous connecter
Pas encore inscrit ? s'inscrire