Pour le groupe Bosch, les données sont au coeur du voyage vers l'industrie du futur
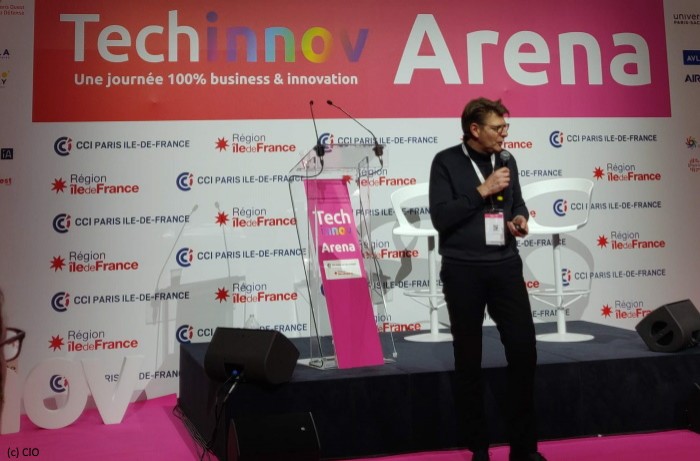
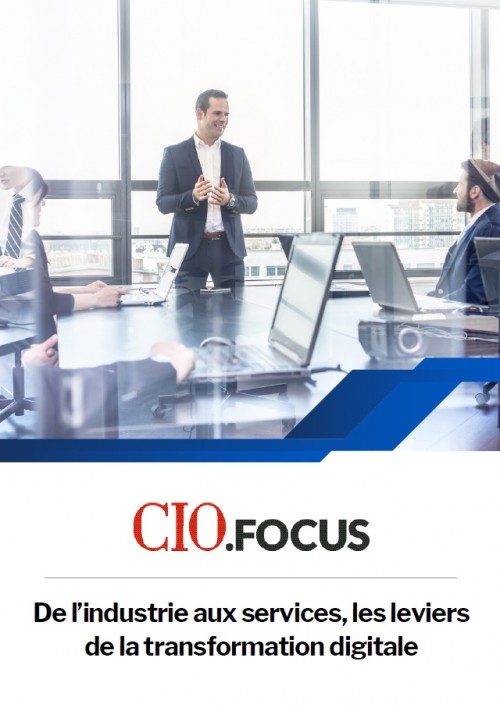
De l’industrie aux services, les leviers de la transformation digitale
Transformation digitale ou transformation numérique ? La question ne porte pas sur le vocabulaire mais sur le périmètre de la transformation. Nous vous proposons dans ce CIO.focus d'en avoir la démonstration au travers de témoignages de DSI d'entreprises aussi bien industrielles que de services....
DécouvrirÀ l'occasion du salon Techinnov, Pascal Laurin, directeur Industrie 4.0 Bosch France et directeur de division chez Bosch Rexroth France, a partagé l'expérience du groupe allemand sur le passage à l'industrie du futur. Un voyage entamé en 2013, qui se poursuit en 2020 et au-delà.
PublicitéGroupe industriel allemand, Bosch a développé sa feuille de route pour l'industrie 4.0 depuis 2013. « Le challenge 4.0 était d'abord un enjeu interne, il s'agissait pour le groupe de transformer son modèle industriel pour être en mesure de s'adapter à la mutation de ses marchés », explique Pascal Laurin, directeur Industrie 4.0 Bosch France et directeur de division chez Bosch Rexroth France. Pour l'industriel, il s'agissait de se repositionner, à la fois pour être en mesure de répondre à la diversité accrue des demandes et pour éviter l'apparition d'intermédiaires entre lui et les donneurs d'ordre. Pour Bosch, équipementier de rang 1 de la filière automobile à travers sa branche mobilité, la relation en direct avec les grands constructeurs tient en effet une place centrale dans son modèle.
« L'industrie 3.0 a permis d'automatiser les chaînes de production, en associant la robotique et les technologies de l'information. L'industrie 4.0 porte quant à elle davantage sur l'IoT, les données et la connectivité », estime Pascal Laurin. En 2013, Volkmar Denner, PDG du groupe, présente sa vision des 3S : « sensors, softwares, services » (capteurs, logiciels et services), affirmant sa volonté de faire de Bosch une entreprise du monde logiciel. Pour sa trajectoire vers l'industrie du futur, le groupe a adopté une approche de l'industrie 4.0 résolument pragmatique. « Pour nous, il s'agit avant tout d'un outil au service de trois grands objectifs : la hausse de la flexibilité et de la rapidité ; l'amélioration de la profitabilité et le maintien de l'emploi et de notre compétitivité », souligne Pascal Laurin. Concrètement, cela signifie par exemple utiliser des solutions comme la maintenance prédictive pour réduire les arrêts de production et améliorer les coûts de possession d'équipements parfois anciens, ou piloter la supply chain et la production grâce au big data pour gagner en transparence et en réactivité. Afin d'être autonome par rapport aux grands acteurs américains, le groupe a également déployé son propre cloud en 2015.
Vers un modèle de « manufacturing-as-a-service »
Pour Bosch, il était plus simple de démarrer la transformation par la partie hardware que par le service. « Nous avons abordé la transformation par l'Internet des Objets (IoT) et les capteurs, car c'est l'un de nos métiers historiques. Nous fabriquons par exemple 4 milliards de microsystèmes électromécaniques (MEMS) par an, utilisés notamment dans les gyroscopes », déclare Pascal Laurin. Cependant, le groupe était convaincu que la combinaison du hardware et du service, grâce au logiciel, pouvait apporter beaucoup de valeur. Au fil des années, Bosch a donc élaboré et mis en place un modèle de « fabrication en tant que service », permettant de répondre aux enjeux précédemment évoqués. À terme, la vision de l'industriel consiste à passer d'une production de masse à une production davantage personnalisée. Le groupe reprend aussi certaines idées dans sa branche Rexroth, qui conçoit et développe des solutions pour les industriels.
PublicitéBosch possède 280 usines dans le monde entier, avec des rythmes et des processus de production très différents. En France par exemple, l'usine de Rodez (12) produit 100 000 injecteurs par semaine, tandis que celle de Drancy (93), Bosch elm.leblanc, fabrique 100 000 chaudières par an. Pour cette raison, la transformation nécessitait de partir du terrain, au plus près des problématiques de chaque site. Dans cette optique, le groupe qui était traditionnellement dans un modèle bottom-up a inversé cette logique, en allant chercher des idées directement dans ses unités de production. « Nous avons demandé aux 280 usines du groupe, qui vont de 200 salariés pour les plus petites à plus de 10 000 sur les grands sites, d'élaborer chacune leur feuille de route pour la transformation digitale, quels que soient leur taille et leurs moyens. » Le but : penser autrement pour identifier de vrais sujets.
Encourager la duplication des projets réussis
En procédant ainsi, le groupe a redonné du pouvoir aux responsables d'usines. Sur plus de 30 000 projets, 3000 sont arrivés à terme, soit 10 projets en moyenne par usine. « Nous avions des exigences précises en termes de retour sur investissement : aucun projet ne devait avoir un ROI supérieur à 24 mois », ajoute Pascal Laurin. Les déploiements ont démarré en 2017 à l'échelle locale. Ensuite, le groupe a récupéré les réussites, et depuis 2018 il les déploie au niveau global. « Nous avons mis en place un prix du 'copier-coller' pour récompenser les usines qui reproduisaient les bonnes idées avec succès », raconte le directeur Industrie 4.0.
Plusieurs projets ont été déployés dans les usines françaises. Membre de l'Alliance Industrie du Futur (AIF) depuis 2015, le groupe a vu trois de ses implantations désignées comme sites vitrine, dont la dernière en date, l'usine de Mondeville (76), a été labellisée en avril 2019. Parmi les projets et technologies mis en oeuvre figurent par exemple des AGV (véhicules autonomes), capables de se réagencer pour créer des lignes de production optimisées, ou encore des systèmes de monitoring de la supply chain au fil de l'eau.
Une culture centrée sur les collaborateurs
Les déploiements s'échelonnent dans le temps, chaque usine choisissant les projets en fonction de son contexte et de ses priorités. Le site de Mondeville a par exemple déployé la supervision en temps réel de la production dès 2012 et les AGV seulement en 2018, au moment où le site a pu identifier un ROI clair. Dans certaines branches d'activité, comme la fabrication de systèmes ABS ou ESP (contrôle électronique de la trajectoire), il existe des usines mères et filles, toutes connectées. Cela a permis d'effectuer des benchmarks, pour savoir où un projet obtenait les meilleurs résultats, afin de comprendre les facteurs de succès et d'améliorer le ROI.
La transition vers l'industrie 4.0 s'est également accompagnée d'un changement de culture. L'évolution du slogan d'employeur du groupe, passant de « We are Bosch » à « We lead Bosch », en témoigne. « Nous avons adopté une culture d'intrapreneuriat », insiste Pascal Laurin. La démarche laisse une large place au travail collaboratif et aux équipes multidisciplinaires, avec des représentants de la logistique, des ressources humaines, des responsables d'usines et des opérateurs de production. « Les collaborateurs sont placés au coeur du sujet, afin de donner du sens à la transformation. Le groupe a mis l'accent sur la montée en compétences des employés et l'identification des talents », détaille Pascal Laurin.
Pour les managers aussi, la transformation a eu un impact important. « Avec l'industrie 4.0, le management devient de moins en moins pyramidal. Il n'y a plus besoin de faire du reporting si les données sont disponibles en temps réel », souligne le directeur Industrie 4.0. « Les managers intermédiaires, qui étaient auparavant dans une position de sachants, sont en train de devenir des sponsors, chargés de libérer la créativité de leurs collaborateurs. »
Des usines capables de se reconfigurer en fonction des commandes
Pour les années qui viennent, le groupe s'oriente vers l'automatisation de l'usine, en réfléchissant à des outils de production très flexibles. « Pour la fabrication de batteries par exemple, nous devons être en mesure de nous adapter. Nous ne savons pas si demain les constructeurs vont privilégier les véhicules hybrides ou le tout électrique », pointe Pascal Laurin.
Pour cela, Bosch investit fortement dans l'intelligence artificielle, à travers un centre dédié, le Bosch Center for Artificial Intelligence (BCAI). Le groupe réfléchit aussi à l'intégration de véhicules automatisés intelligents (AIV) et de la 5G dans ses usines et dans ses solutions. Enfin, il développe des technologies de sols intelligents, où la connectivité et l'alimentation en énergie sont intégrées. « Cela permettrait de concevoir des ateliers de production capables de se reconfigurer pendant la nuit, en fonction des commandes qui arrivent dans le système ERP », décrit Pascal Laurin. « Ces démarches favorisent des usines de plus petite taille, capables de fabriquer une plus grande diversité de produits ». À l'heure où la réindustrialisation des territoires redevient une priorité, « l'industrie 4.0 facilite les relocalisations », conclut-il.
Article rédigé par

Aurélie Chandeze, Rédactrice en chef adjointe de CIO
Suivez l'auteur sur Linked In,
Commentaire
INFORMATION
Vous devez être connecté à votre compte CIO pour poster un commentaire.
Cliquez ici pour vous connecter
Pas encore inscrit ? s'inscrire