Antartic II (groupement Agromousquetaires) partage son expérience sur la mise en oeuvre d'un MES
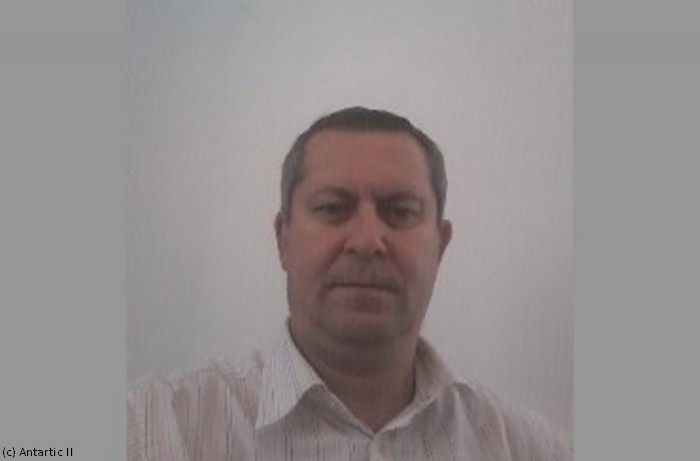
L'usine agroalimentaire Antartic II, rattachée au groupement AgroMousquetaires (rattaché au Groupement des Mousquetaires, dont l'enseigne majeure est Intermarché) a déployé le système de pilotage de production Sedapta Quartis il y a quelques années. Lors d'un webinaire organisé par l'éditeur, le chef de projet SI de la société est revenu sur ce projet et sur les enseignements tirés.
PublicitéCréée en 1986, Antartic II est l'une des unités de production de la filière épicerie du groupement Agromousquetaires, le pôle agroalimentaire du Groupement des Mousquetaires (enseigne Intermarché notamment). Cette usine située en Ardèche fabrique 1300 références de produits finis, appartenant à différentes catégories de produits secs. En 2013, dans le cadre d'un plan d'excellence opérationnelle, la société a décidé de mettre en place un système de pilotage de la production ou MES (manufacturing execution system) pour remplacer un outil de gestion de la production (GPAO) en voie d'obsolescence. L'usine a retenu la solution Quartis de Sedapta. Le 23 février 2021, lors d'un webinaire, Damien Bertrand, chef de projet SI filière épicerie chez Agromousquetaires a partagé l'expérience tirée de ce projet.
« Dans le cadre de notre plan quinquennal 2010-2015, nous avions prévu de mettre en place un nouvel ERP, la solution Sage X3 », se souvient Damien Bertrand. Toutefois, la solution de GPAO en place n'était pas intégrée à celui-ci et ne permettait pas d'avoir une vision précise et en temps réel des ordres de fabrication (OF) et de la consommation de matières associées. Par ailleurs, le site n'utilisait pas de codes-barres à l'époque, ce qui compliquait encore le suivi. « Les caristes partaient à leur poste avec des piles de papier », confie le chef de projet SI. Au même moment, le groupement Agromousquetaires avait lancé un plan d'excellence opérationnelle, dénommée « Ensemble vers l'excellence », visant à améliorer le suivi industriel et à mieux piloter les pertes de matières. Dans ce contexte, Antartic II a donc décidé de s'équiper d'un MES. « Nous souhaitions maîtriser notre consommation de matières et d'emballages, mais aussi améliorer notre taux de rendement synthétique (TRS) », explique Damien Bertrand.
Un système ouvert
La société a alors entamé une étude des solutions MES existantes, avec plusieurs attentes. L'outil devait permettre de suivre précisément les différents types de stocks. Il devait également faciliter la traçabilité des lots, un impératif réglementaire dans l'industrie agroalimentaire, ainsi que les contrôles qualité, jusqu'alors réalisés sur papier. La solution devait aussi contribuer à la maîtrise des procédés de fabrication (les recettes) et au suivi des pannes. Il fallait également qu'elle fournisse un certain nombre d'indicateurs : quantités produites, TRS par OF et par équipe, matières consommées par OF, ligne ou atelier, etc. Enfin, elle devait permettre de numériser au maximum tous les documents et procédures en lien avec la production. Pour répondre à ces besoins, l'outil devait donc être capable de se connecter à de nombreuses solutions externes, afin de collecter et de transmettre des informations.
PublicitéÀ l'issue de cette étude du marché, la société a retenu la solution MES Quartis de Sedapta. « L'une des raisons de notre choix est qu'il s'agissait d'un système ouvert », indique Damien Bertrand. La solution a été déployée dans les cinq ateliers du site et interfacée avec le système ERP. « Le MES est central, beaucoup d'outils communiquent avec lui et il remonte ensuite les informations à X3 », souligne le chef de projet SI. Au total, le MES est interfacé avec huit environnements différents : l'ERP sage X3 bien sûr, mais aussi les terminaux tactiles des opérateurs, des lecteurs de codes-barres mis en place au moment du projet, les balances fixes et mobiles, les gestionnaires des imprimantes qui assurent l'étiquetage et divers automates et machines installés sur les lignes et dans les ateliers. En 2016, la solution a également été interfacée avec la solution de gestion de la maintenance (GMAO) du site, un outil de Carl Software. Enfin, des terminaux industriels TCL 17 et 21,5 de Sedapta Osys ont été installés directement dans les ateliers.
Support à l'amélioration continue
La solution affiche aujourd'hui les ordonnancements et les plannings hebdomadaires du personnel directement sur les écrans, assurant ainsi les salariés de disposer d'une information à jour. Elle permet aussi aux opérateurs de connaître en temps réel la performance des lignes et leur remonte des alertes. « Au départ, notre but principal était d'acquérir des données, mais assez vite nous avons réalisé qu'il fallait restituer ces informations aux opérateurs, de façon très visuelle, afin de les inciter à remplir les éléments nécessaires », fait observer Damien Bertrand. Parmi les fonctionnalités proposées par le MES figurent par exemple des écrans pour gérer les ordres de fabrication, depuis le début jusqu'à la fin de l'opération. L'outil permet également de déployer des autocontrôles qualité : les opérateurs doivent répondre à quelques questions simples pour s'assurer que les procédures en place sont respectées. En cas d'aléas, l'outil leur permet d'expliquer les problèmes rencontrés. Ces informations sont ensuite analysées de façon systématique par le laboratoire qualité. Antartic II a aussi déployé un système de reporting pour suivre la performance par atelier, avec des indicateurs en temps réel et au lendemain destinés aux superviseurs.
Depuis la mise en place du MES, celui-ci s'est révélé être un vrai support à la démarche d'amélioration continue de l'usine. Si le retour sur investissement précis est difficile à calculer, les gains étant de plusieurs ordres, certains bénéfices ont rapidement été mesurés. En 2015, la société a ainsi estimé que la solution lui avait permis de réduire ses pertes de matières de près de moitié, celles-ci étant passées de 1 million à 500 000 euros. Concernant la digitalisation, le chef de projet SI considère que l'objectif de supprimer totalement le papier est un peu utopique, toutefois le MES a permis de réduire considérablement ces flux et les saisies manuelles associées. Le MES représente surtout pour la société un outil d'animation, de mesure et de pilotage, qui aide l'usine à définir des plans d'action. En 2015, la mise en oeuvre de ces plans d'action a permis de gagner près de100 000 €.
Le MES est un outil vivant
Rétrospectivement, Damien Bertrand a identifié plusieurs facteurs clefs de succès pour ce projet, ainsi que quelques recommandations. Tout d'abord, il est impératif selon lui de considérer le déploiement d'un MES comme un projet d'entreprise, dans lequel les toutes les équipes sont impliquées dès le départ : production, qualité, sécurité et contrôle de gestion industriel. « Le MES est leur outil », rappelle le chef de projet SI. « Il faut être à l'écoute des opérateurs et de leur ressenti, pour simplifier les écrans et les guider au maximum », conseille-t-il. La mise en place d'une telle solution demande du temps, il faut donc une équipe projet disponible dans la durée. Il souligne également qu'un MES est un outil vivant, qui évolue pratiquement au quotidien pour s'adapter aux changements dans les processus, la réglementation, les recettes... Pour que les données soient bonnes, il note également qu'il faut de la rigueur dans les saisies. Dans ce but, il recommande d'encadrer et de vérifier celles-ci, en mettant en place des contrôles appropriés dans l'outil. Il pointe également l'importance de bien délimiter les périmètres respectifs du MES (TRS, suivi des pertes, etc.) et de l'ERP (gestion, référentiel). Enfin, pour qu'un tel projet contribue réellement à l'amélioration de la performance, Damien Bertrand note un prérequis essentiel : « il faut déjà une certaine maturité de l'organisation et de ses processus pour envisager de digitaliser ces derniers. »
Article rédigé par

Aurélie Chandeze, Rédactrice en chef adjointe de CIO
Suivez l'auteur sur Linked In,
Commentaire
INFORMATION
Vous devez être connecté à votre compte CIO pour poster un commentaire.
Cliquez ici pour vous connecter
Pas encore inscrit ? s'inscrire